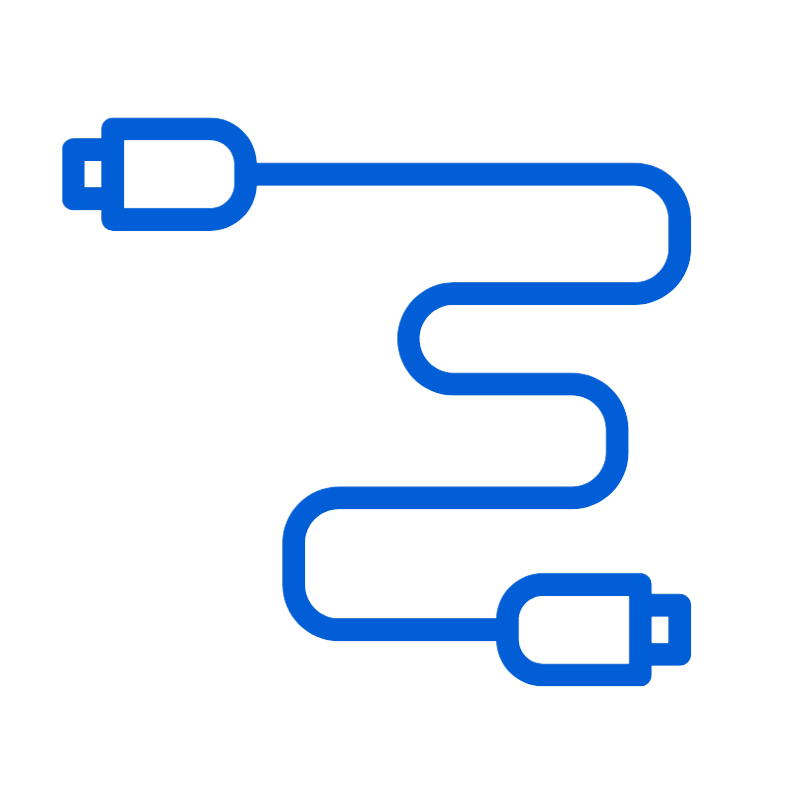
HyperCONN
Connectors for Data Integration with Industry 4.0 Machines and Devices
HyperCONN is a software solution designed for integrating Industry 4.0 machines and devices. It connects industrial hardware with enterprise information systems, enabling data extraction and process analysis.
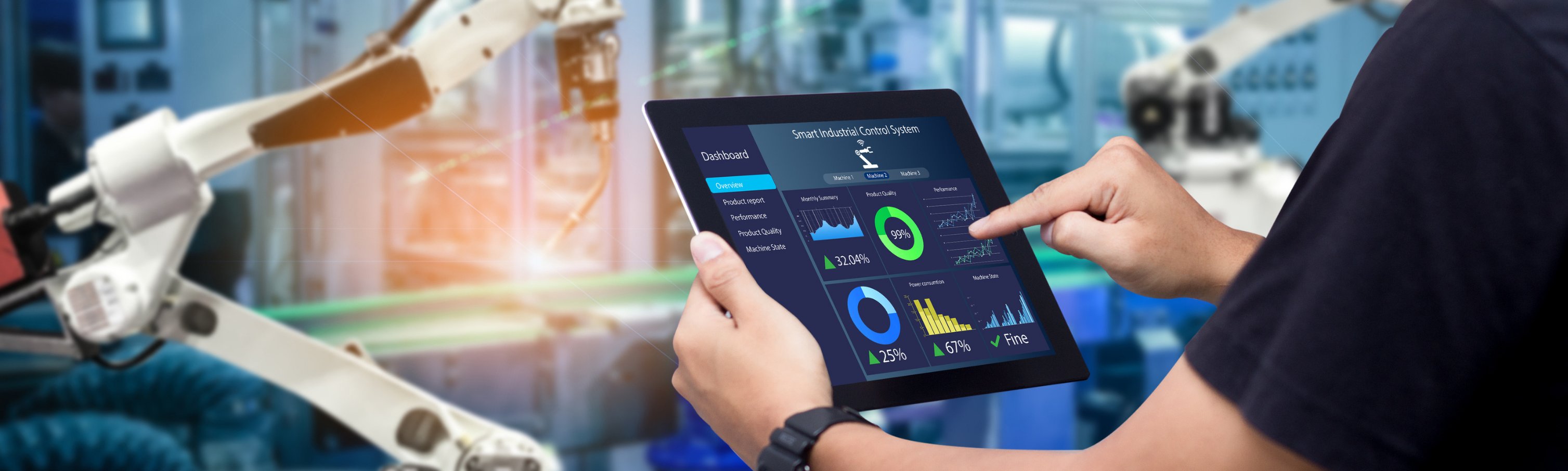
Customized Interconnection
Connectors developed ad hoc to adapt to the specific protocols and standards of each machine (e.g., MODBUS, OPC/UA).
Enhancing Production Data
Data collection and utilization for real-time monitoring and strategic and managerial analysis.
What HyperCONN Offers:
Integration with machines and devices
Process data collection
Real-time monitoring
Advanced KPI analysis
Customization of connection protocols
Support for sensors and technical measurements
Key Features
Customized Connectivity
Implements ad hoc connectors to integrate specific machines with enterprise information systems
Process Data Extraction
Enables the collection of operational data such as production volumes, scraps, and completed work orders
Support for Standard Protocols
Manages protocols such as MODBUS and OPC/UA to ensure machine interoperability with enterprise systems
Real-Time Monitoring and Analysis
Allows real-time visualization and data utilization to optimize production and managerial control
HyperCONN Also Enables:
- Maximizing the Value of Industry 4.0 Machine Data: Prevents the underutilization of the potential of connected devices.
- Support for Managerial Analysis: Facilitates the calculation of costs per unit and the evaluation of business performance.
- Optimization of Production Control: Provides detailed insights into production phases and operational issues.
- Access to Experts for Tailored Projects: A team of consultants available to design customized solutions for each company.